The manufacturing industry is experiencing unprecedented challenges when it comes to attracting and retaining skilled talent. While the sector remains the backbone of economies worldwide, a shifting labor landscape and growing skills gap are making it increasingly difficult for manufacturers to find and keep the right people.
With workforce shortages anticipated to reach 2.1 million unfilled jobs by 2030 in the U.S. alone, building a solid recruiting and retention strategy has never been more important. Manufacturers who actively prioritize workforce solutions will not only ensure continuous production but also position themselves to grow and thrive.
Understanding the Manufacturing Skills Gap
What is the Manufacturing Skills Gap?
The “skills gap” refers to an imbalance between the skills that employers need and the expertise the workforce can provide. For manufacturing, this means an increasing shortage of candidates who are equipped to handle advancements such as automation, robotics, and smart technologies. Traditional manufacturing skills are no longer enough for an increasingly data-driven industry.
Root Causes of the Skills Gap
- Technological Transformation
The rise of Industry 4.0 has driven manufacturers to embrace automation, robotics, and advanced digital systems to improve efficiency and productivity. However, this rapid technological shift has exposed a significant challenge—many workers lack the necessary training and skills to effectively operate and manage these advanced technologies. As a result, there is a growing gap in the talent pool, leaving industries struggling to find qualified professionals who can keep up with the demands of this new era in manufacturing.
- Generational Shift
A wave of retirements from the Baby Boomer generation is rapidly depleting the industry’s knowledge base, creating a significant skills gap that’s difficult to fill. Gen Z now makes up a significant portion of the global workforce, in 2030, we’ll see Generation Z constitute about 30% of the workforce. This group brings a new set of skills and expectations to the table, which will impact how industry leaders approach workforce management.
- Decline in Vocational Training
Many schools have shifted their focus away from trade and technical training programs, placing greater emphasis on academic and college-preparatory courses instead. Despite a recent 3 percent rebound in vocational enrollment (up from 2018 levels), a survey of 1,000 US-based 18- to 20-year-olds found that 74 percent perceive a stigma associated with choosing vocational school over a traditional four-year university. This has led to a growing shortage of entry-level workers with the relevant expertise to fill these in-demand roles, creating long-term challenges for industries reliant on skilled labor.
The Impact on Businesses
Without a clear strategy to address the skills gap, manufacturers risk facing reduced productivity, higher operational costs, and missed growth opportunities. As technology evolves and industries become more competitive, the need for a skilled workforce has never been greater. Bridging this gap is not just about filling vacant positions; it’s about equipping employees with the knowledge and tools they need to adapt and drive innovation. Taking proactive steps to close the skills gap is essential for ensuring long-term success and maintaining a competitive edge in the market.
Attracting Top Manufacturing Talent
Attracting skilled professionals in manufacturing requires strategic planning and a modern approach. To stand out in a competitive hiring market, manufacturers should adopt targeted recruitment strategies. This includes using niche platforms like job boards, trade-specific websites, and local community outreach programs to connect with manufacturing professionals.
Personalizing outreach is also key—highlighting career growth, advancement opportunities, and training programs can make a big impact. Engaging passive talent through social media and networks like LinkedIn allows employers to reach candidates who aren’t actively job hunting.
Technology is essential for modern recruitment, streamlining the process and improving efficiency. AI-driven platforms and tools quickly analyze resumes to identify top candidates. Predictive analytics help determine which candidates are likely to succeed in a role, while automated tools like chatbots ensure ongoing engagement with candidates, saving time and effort.
Employer branding is more important than ever. Glassdoor reports that 86% of job seekers research a company’s reputation before applying. A strong employer brand—built by showcasing team success, diversity efforts, sustainability, and innovation—attracts top talent and builds trust in the manufacturing industry.
Retaining Existing Manufacturing Talent
Retaining top talent is essential for long-term success, and it begins with creating an environment where employees feel valued, heard, and supported. Once talented individuals join your organization, effective retention strategies ensure they stick around.
A strong onboarding and training program is a critical first step. Onboarding should go beyond administrative tasks, helping new hires feel acclimated and empowered from day one. Job-shadowing opportunities with seasoned employees can provide valuable hands-on learning experiences, while continuous learning opportunities such as certifications and training programs help employees grow alongside technological advancements. Regular feedback sessions also play an important role, ensuring employees have the support and tools they need to succeed.
Offering competitive compensation and benefits is another cornerstone of retention. Fair and attractive compensation can make all the difference in keeping qualified employees engaged. Performance bonuses can serve as powerful incentives for exceptional work, while flexible schedules or remote work options help accommodate diverse needs. Comprehensive benefits packages, including health care, retirement plans, and wellness perks, show employees that their well-being is a priority.
Lastly, building a positive company culture is vital for employee satisfaction. A culture rooted in inclusivity and diversity fosters unity within teams and ensures everyone feels valued. Celebrating milestones and achievements boosts morale, while creating an environment where employees are encouraged to take initiative but still feel supported by leadership helps them thrive. Together, these strategies create a workplace where employees want to grow and stay for the long term.
Overcoming Challenges in Talent Acquisition
Addressing the Skills Gap with Education Programs
Manufacturers face a growing challenge in bridging the skills gap, making it crucial to build strong partnerships with educational institutions. Collaborating with these institutions can help champion impactful solutions that prepare the next generation of workers for success in the industry, such as:
- Apprenticeships: Encourage hands-on learning by partnering with vocational schools and community colleges to create programs tailored to the specific needs of manufacturing. These programs provide students with real-world experience, helping them develop practical skills and a deeper understanding of the industry.
- Scholarships and Grants: Support students pursuing STEM-related careers by offering financial aid that makes education more accessible. By investing in future talent, manufacturers can create a steady pipeline of skilled workers ready to tackle the challenges of a rapidly evolving industry.
- Upskilling Opportunities: Provide current employees with ongoing training programs to help them adapt to new technologies and industry advancements. This not only boosts employee confidence and productivity but also ensures the business remains competitive in an ever-changing landscape.
Using Workforce Management Solutions
In addition to addressing education and training, manufacturers can benefit greatly from sophisticated workforce management solutions to overcome labor challenges. These tools bring efficiency and insight, enabling organizations to:
- Predict labor demand during peak seasons: Accurately forecast workforce needs to ensure operations run smoothly, especially during high-demand periods. This minimizes bottlenecks and ensures timely production.
- Monitor performance metrics and adjust strategies accordingly: Gain valuable insights into workforce performance and efficiency. By analyzing data, manufacturers can identify areas for improvement and refine their strategies to meet organizational goals.
- Track and optimize employee satisfaction levels to reduce turnover rates: High turnover can be costly and disruptive. Workforce management tools can help manufacturers measure employee satisfaction and engagement, addressing concerns proactively to foster a motivated and loyal workforce.
By combining educational initiatives with advanced workforce management tools, manufacturers can build a resilient, skilled workforce capable of meeting the demands of the modern industry.
The Future of Manufacturing Talent
Manufacturers must be agile, adaptive, and forward-thinking in their workforce strategies, with HR leaders taking the lead in driving initiatives that blend technology with personal connection. The future of talent retention depends on creating a workplace that balances innovation with genuine care for employees.
As the manufacturing landscape evolves rapidly, addressing the skills gap will be crucial to maintaining competitiveness. By adopting data-driven recruitment strategies, enhancing employer branding, and implementing people-focused retention programs, companies can build the skilled workforce they need. For those in manufacturing struggling to attract and retain talent, these approaches provide a strong foundation.
To learn more about the trends impacting the manufacturing and supply chain industries in 2025, download A Strategic Vision for 2025 and equip yourself with the tools to thrive.
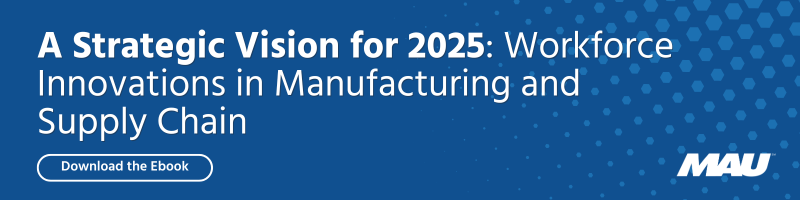